With the purpose of rationalising the manufacturing process of its broad range of customisable products, Oglaend System, the market leader in multidiscipline support and containment systems, decided to invest in an automated welding solution with intelligent fixture technology from Migatronic Automation.
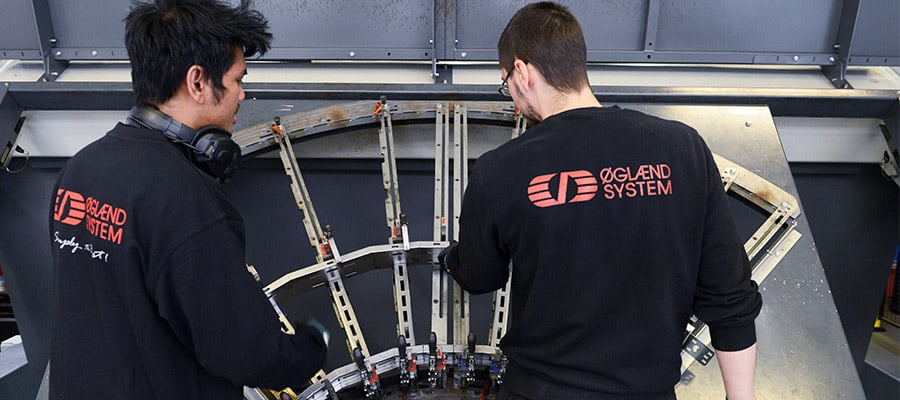
The challenge of high volume customisation
Oglaend System develops, manufactures and sells a broad range of products in the category of multidiscipline support and containment systems, cable trays and cable ladders for customers within the industries of oil and gas, infrastructure, shipbuilding, wind energy, clean room and water treatment.
Every product is customisable to the specific needs of the customers in terms of design and sizing, which places heavy demands on the versatility and intelligence of the company’s high volume manufacturing. In order to cope with the great variation in the product specifications, Oglaend System relied primarily on manual welding at the factory in Klepp.
“Automated welding solutions are by no means new to our manufacturing process. Yet we did not know of a flexible and intelligent automated solution that could solve the challenge of our customers’ varied product demands. The welding fixtures constituted the main issue in this regard, and we had invested in several welding fixtures in the past without any practical results – which is why we resorted to manual welding at the time“, Benjamin Ganic, supervisor and welding coordinator at Oglaend System, says.
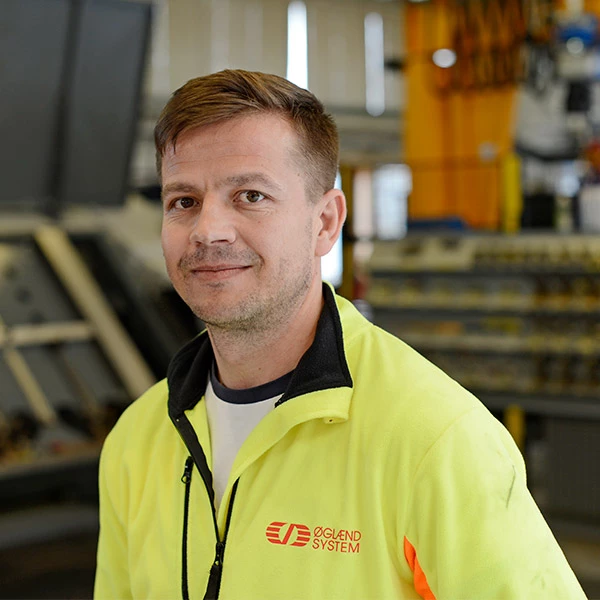

To stay competitive
Oglaend System was in no doubt that relying on manual welding for high-volume manufacturing was not a viable option:
“We knew that some form of automated solution was needed in order to keep up with demand and stay competitive. But acquiring an automated solution is not only important to production efficiency, costs and uniformity in welding finish. It is also about taking care of our manufacturing workers by relieving them from a high degree of manual labour“, Benjamin Ganic says.
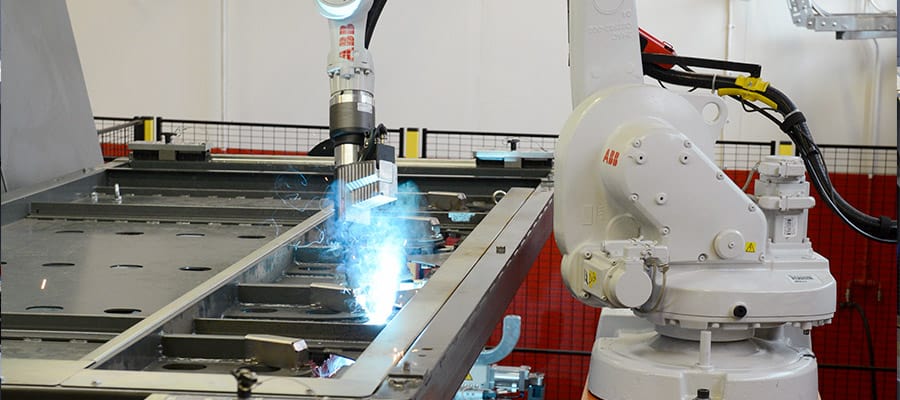
The parent-subsidiary relationship
The parent company, Migatronic, being already among Oglaend System’s suppliers of manual welding machines, arranged the initial contact between the subsidiary, Migatronic Automation, and Oglaend System.
“The Migatronic Group has established a good reputation among the manufacturing companies in our area, and we have been very pleased with our relationship through the years. So when it came to our attention that Migatronic Automation possessed the know-how and skills needed to develop an intelligent automated solution tailored for our needs, we were of course interested“, Benjamin Ganic says.
“We were initially invited to visit Migatronic Automation and one of its customers in our local area, where we saw one of its compelling automated welding solutions. The system demonstration and the concurrent counselling gave us full confidence in the investment process – and from that point, we began our close partnership with Migatronic Automation“, he continues.
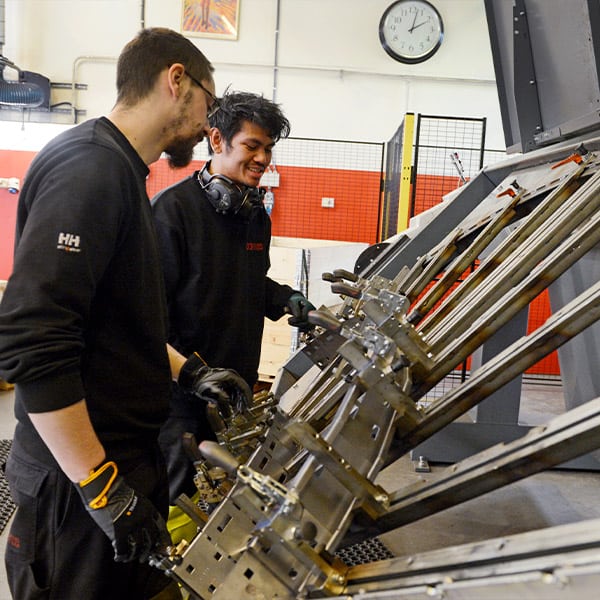
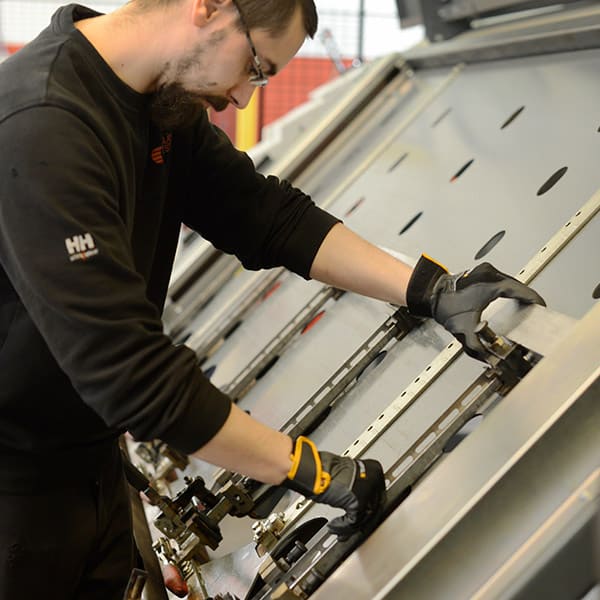
Intelligent welding fixtures
Migatronic Automation focused on presenting Oglaend System with an automated solution that would accommodate the company’s main issue relating to the welding fixtures:
“We developed what we refer to as ‘intelligent welding fixtures’, which enable the manufacturing workers at Oglaend System to easily adjust the automated welding system to effectively handle workpieces with multiple variations in shapes and sizes – all by the press of a button. In this case, we have developed an equally advanced piece of custom-made software as well as welding hardware“, Claus Pagh, Sales Director of Migatronic Automation, explains.
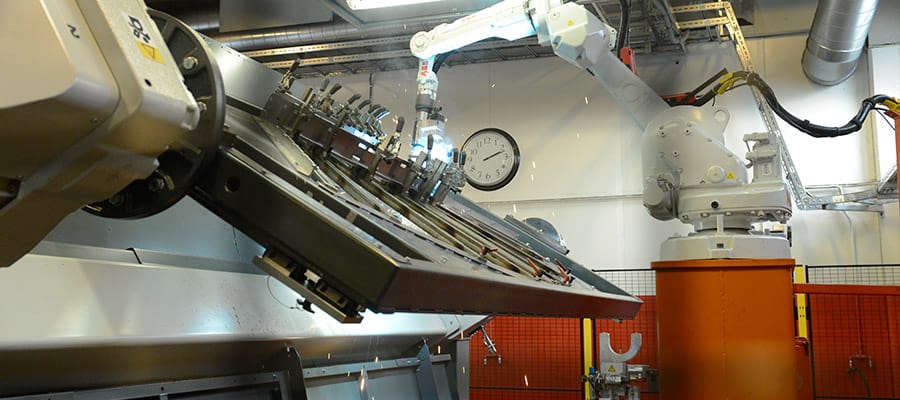
More than a supplier
According to Benjamin Ganic, both the new automated welding solution and the process leading up to its development have been very rewarding for the Norwegian company:
“Not only have we rationalised our manufacturing process through automation, and increased our productivity in a way that we did not think possible. But we have also learned a lot about welding by engaging in a collaboration with Migatronic Automation. Needless to say, we are very pleased with our partnership and the automated solution that they have provided us with“.
Consulting engineers
It coincides well with the very aim of Migatronic Automation, which is to be considered as consulting engineers that cooperate with its customers in developing the best possible automated solution:
“We have created a unique automated solution tailored specifically for the needs of Oglaend System. It emphatically optimises its manufacturing process from the moment it is installed, as it automates a production line that used to operate manually. That is essentially what our work is all about – and we are always happy to see our technology adding significant value to the customer“, Claus Pagh concludes.