Every vessel in the world depends on temperature sensors in engines and machinery to be efficient at sea. They measure air and liquid temperature or solid matter.
Danfoss Sensing Solutions designs and produces industrial temperature sensors for all marine applications.
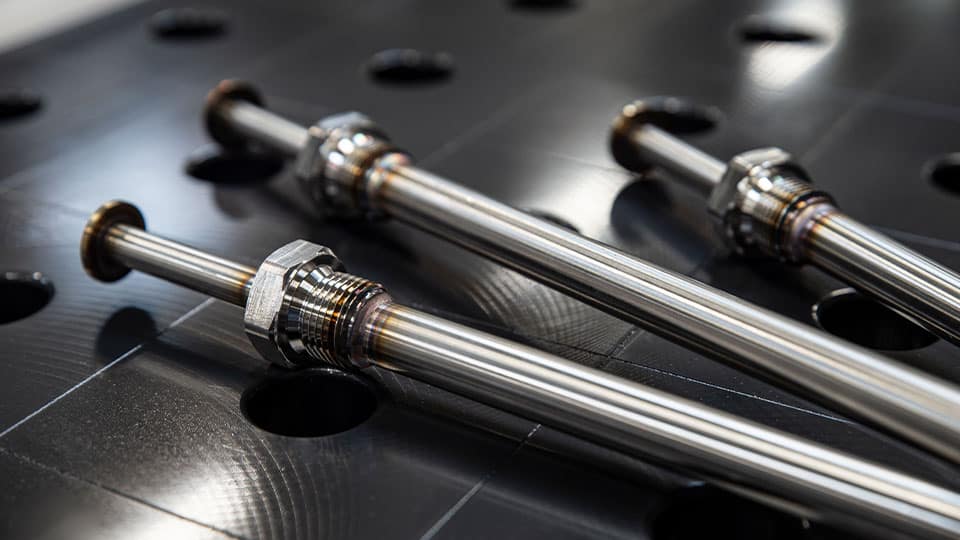
An automated welding solution has streamlined the production of sensors, reduced the risk of errors, and improved the quality.
Challenge
Every component for temperature sensors consists of various sub-components and has up to six welds. All welds needed manually performed individual measuring and evaluation. That was a time-consuming process with a high risk of errors.
Solution
The solution with an industrial robot and a TIG welding power source finishes all weld seams on a component in a single program. The operator collects the sub-components, places them in the robot cell and chooses a program. The welding process is fully automatic.
Result
By relying on a fully automatic welding solution, the production of temperature sensors is less dependent on the operator. It improves repeatability, uniformity, and weld quality. It minimises the risk of errors and increases supplier reliability.
Optimising the production process minimises risk
For Danfoss Sensing Solutions, it is all about the process. The high demand for accuracy placed a large responsibility on the welders’ performances. Only a small deviation and the complete component had to be discarded. That made the process risky and less reliable.
By automating the welding of components for temperature sensors, the production process becomes less dependent on the operator. That minimises the risk of errors and increases production reliability and repeatability. Also, there is no unnecessary handling and treating of components. Instead, every component is treated efficiently and with exactly the same precision.
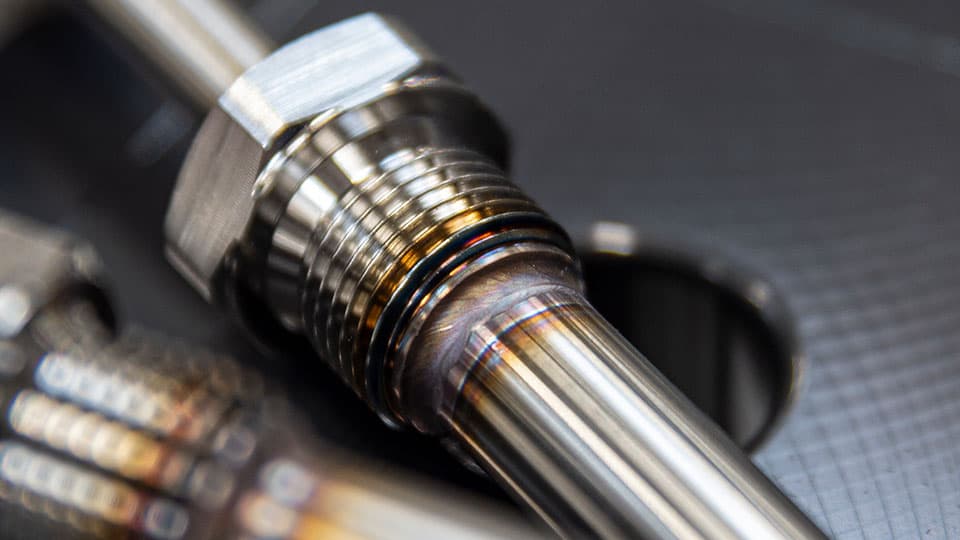
“It is very important for us to minimise risk. We can do that by making the production less dependent on manual labour. Especially if employees need specialised knowhow to carry out the job. The market for temperature sensors is tough. We need to optimise the production to become an even more reliable supplier. By improving reliability, we become more attractive in the market.”
Jacob Friis-Rasmussen, Process Technology Engineer, Danfoss Sensing Solutions
High quality demands makes automation an attractive investment
Manual welding processes will always entail some kind of varying quality. The new TIG welding solution can weld 160 different compilations of components for temperature sensors. All programs are optimised to spend the least time on each component.
Advanced fixtures with several axes and motors will automatically be adjusted to each of the 160+ components.
A laser scanner takes potential tolerances generated from previous welds into account. If it finds any, it will adjust the welding of the current workpiece down to tenth of a millimetre. In that way, all weld seams will be placed extremely precisely.
“I know good quality when I see it. I have worked with temperature sensors for many years, and I know how difficult some of the welds can be. The level of accuracy is impressive. This TIG robot cell has improved the welding quality because of the extremely precise welds. We can definitely deliver the high level of quality that we require.”
Sten Davidsen, Project Engineering, Danfoss Sensing Solutions
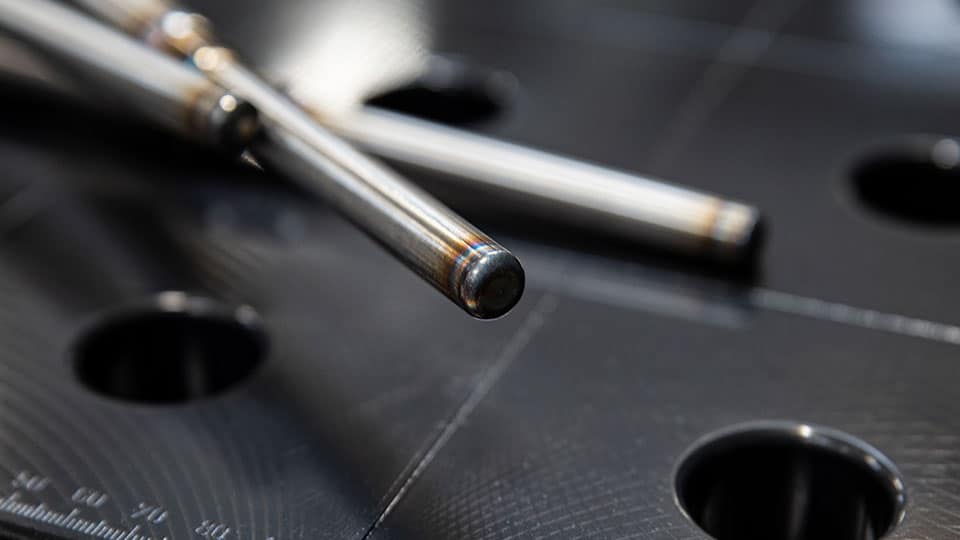