Welding automation is a process that helps to automate welding tasks. It involves the use of specialized equipment, software, and devices that work together to enhance the welding process. By automating welding tasks, companies can achieve a higher level of efficiency, precision, and quality.
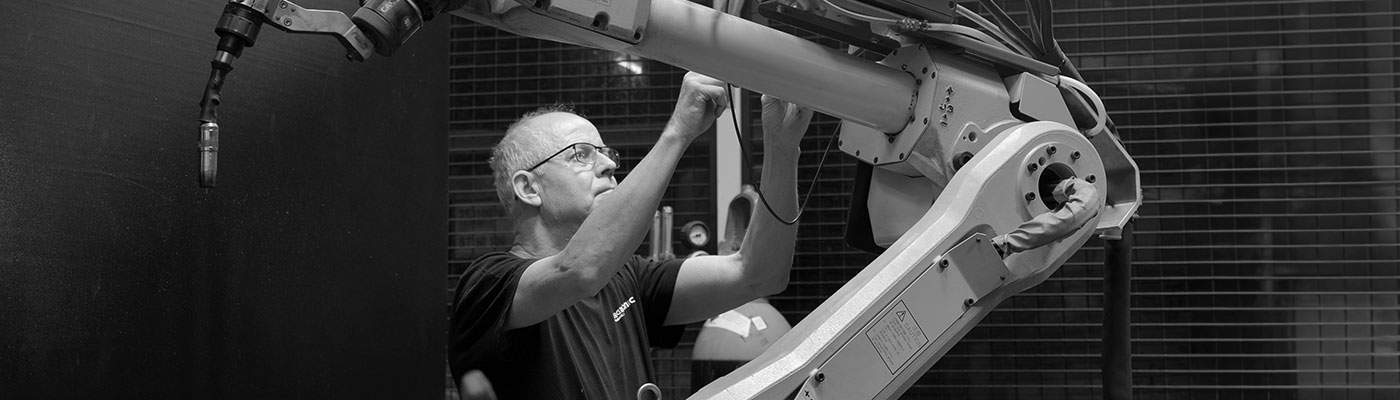
The fundamentals of welding automation include the use of robotic arms, welding sensors, and computer software to control the welding process. These components work together to ensure that the welding process is accurate and consistent. Welding automation can be used for various welding tasks, including spot welding, arc welding, and gas welding.
One of the primary benefits of welding automation is that it can save time and reduce costs. Automated welding systems can work around the clock, which means that companies can produce more products in less time. Additionally, welding automation can reduce the need for manual labor, which can help to reduce labor costs.
Key Takeaways
- Welding automation involves the use of specialized equipment, software, and devices to automate welding tasks.
- The fundamentals of welding automation include robotic arms, welding sensors, and computer software.
- Welding automation can save time and reduce costs for companies.
Fundamentals of Welding Automation
Definition and Concepts
Welding automation is the use of machines and robots to perform welding operations with minimal or no intervention from operators. This includes the entire welding process, from loading and unloading the parts to be welded, to positioning the parts, to welding them together, in complex processes. Welding automation is designed to increase the speed, precision, quality, and consistency of welds compared to manual welding.
Welding automation systems can be customized to meet the specific needs of a given process. The best and most efficient automated welding systems are designed specifically to the process and aren’t cookie-cutter solutions. Common types of welding automation include robotic welding, automated welding cells, and automated welding machines.
History and Evolution
Welding automation has been around for over 50 years and has evolved significantly since its inception. The first welding robots were introduced in the 1960s and were used primarily in the automotive industry. Today, welding automation is used in many industries, including aerospace, construction, shipbuilding, and more.
Advancements in technology have made welding automation more efficient and cost-effective. Welding robots are very precise, move smoothly, and can work at high speeds, making them ideal for mass production and high-volume welding. Automated welding machines have also become more advanced, with features such as touch screen controls, automatic wire feeders, and real-time monitoring of the welding process.
In conclusion, welding automation is an essential tool for industries that require high-volume welding or complex welding processes. With its ability to increase speed, precision, and quality, welding automation is becoming more prevalent in many industries.
Types of Welding Automation
Welding automation can be classified into four main types: fixed automation, programmable automation, flexible automation, and adaptive control systems.
Fixed Automation
Fixed automation is a type of welding automation that is designed for high-volume production. In this type of automation, the welding process is completely automated, and the system is designed to produce a single product or part. The equipment used in fixed automation is usually expensive and requires a high level of maintenance.
Programmable Automation
Programmable automation is a type of welding automation that is designed for medium-volume production. In this type of automation, the welding process is semi-automated, and the system is designed to produce a variety of products or parts. The equipment used in programmable automation is less expensive than fixed automation, and it can be reprogrammed to produce different parts.
Flexible Automation
Flexible automation is a type of welding automation that is designed for low-volume production. In this type of automation, the welding process is semi-automated, and the system is designed to produce a variety of products or parts. The equipment used in flexible automation is less expensive than programmable automation, and it can be easily reconfigured to produce different parts.
Adaptive Control Systems
Adaptive control systems are a type of welding automation that uses feedback control to adjust the welding process in real-time. This type of automation is designed to compensate for variations in the welding process, such as changes in the material properties or welding conditions. Adaptive control systems can improve the quality and consistency of the welding process, and they are particularly useful for welding complex parts or materials.
Overall, the choice of welding automation depends on the production volume, product variety, and required precision. Fixed automation is suitable for high-volume production, while programmable and flexible automation are suitable for medium- and low-volume production, respectively. Adaptive control systems are useful for improving the quality and consistency of the welding process.
Components of Welding Automation Systems
Welding automation systems are composed of several components that work together to automate the welding process. These components include welding robots, positioners and manipulators, sensors and controllers, and software and programming.
Welding Robots
Welding robots are automated machines that are programmed to perform welding tasks. They can be programmed to perform a wide range of welding tasks, from simple spot welding to complex welding operations. Welding robots are equipped with a robotic arm that can be programmed to move in any direction and can be fitted with different welding tools and equipment.
Positioners and Manipulators
Positioners and manipulators are used to position and move the workpiece during the welding process. They are designed to hold and manipulate the workpiece in the correct position and orientation, so that the welding robot can perform the welding operation accurately and efficiently. Positioners and manipulators are available in different sizes and configurations, and can be customized to suit specific welding applications.
Sensors and Controllers
Sensors and controllers are used to monitor and control the welding process. They are designed to detect and measure different parameters such as temperature, voltage, and current, and can be programmed to adjust the welding parameters accordingly. Sensors and controllers are critical components of welding automation systems, as they ensure that the welding process is performed accurately and consistently.
Software and Programming
Software and programming are used to program and control the welding robot and other components of the welding automation system. The software allows the user to create and edit welding programs, set welding parameters, and monitor the welding process. Programming is a critical component of welding automation systems, as it allows the user to customize the welding process to suit specific welding applications.
In summary, welding automation systems are composed of several components that work together to automate the welding process. These components include welding robots, positioners and manipulators, sensors and controllers, and software and programming. Each component plays a critical role in ensuring that the welding process is performed accurately and efficiently.
Benefits of Welding Automation
Welding automation offers a wide range of benefits that can help improve the productivity, quality, safety, and cost-effectiveness of the welding process. Below are some of the key benefits of welding automation:
Increased Productivity
One of the primary benefits of welding automation is increased productivity. Automated welding systems can perform welding tasks much faster than manual welding, which can significantly increase the output of the welding process. According to Miller Welds, an optimized automated welding system can produce a three-to-one output improvement over a human operator.
Improved Quality
Automated welding systems can also improve the quality of welds. Weld quality consists of two factors: weld integrity and repeatability. Automated welding systems ensure weld integrity through electronic weld process controllers. Welding automation can also improve repeatability by ensuring that the welding process is consistent and repeatable, which can help reduce defects and improve overall product quality.
Enhanced Safety
Welding automation can also enhance safety in the welding process. Automated welding systems can perform welding tasks in hazardous environments, which can help reduce the risk of injury to human operators. Additionally, welding automation can reduce the amount of manual handling required in the welding process, which can help reduce the risk of musculoskeletal disorders and other injuries.
Reduced Costs
Finally, welding automation can help reduce costs in the welding process. On average, labor accounts for approximately 70% of any welded part’s cost. Automation can reduce that cost, as a welding robot can typically do the work of two to four people. According to Miller Welds, companies cannot, however, simply purchase an automated welding system and let it go. Instead, they must invest in training and maintenance to ensure that the system is operating at peak efficiency.
Applications of Welding Automation
Welding automation has numerous applications in various industries, including manufacturing, automotive, aerospace and defense, shipbuilding, and marine. Below are some examples of how welding automation is used in these industries.
Manufacturing Industry
The manufacturing industry is one of the largest users of welding automation. Welding robots are used to weld various components, such as chassis, frames, and body panels. Welding automation increases productivity, reduces labor costs, and ensures consistent quality.
Automotive Sector
In the automotive sector, welding automation is used to weld various components such as exhaust systems, suspension systems, and body panels. Welding robots are programmed to weld the components with high precision, ensuring consistent quality. Welding automation also helps to reduce production time and labor costs.
Aerospace and Defense
In the aerospace and defense industries, welding automation is used to weld various components such as fuselage sections, engine components, and landing gear. Welding automation ensures consistent quality and reduces the risk of defects. Welding robots are also used to weld components in hard-to-reach areas, which are difficult for human welders to access.
Shipbuilding and Marine
In the shipbuilding and marine industries, welding automation is used to weld various components such as hulls, decks, and bulkheads. Welding robots are used to weld components in tight spaces and hard-to-reach areas, which are difficult for human welders to access. Welding automation ensures consistent quality and reduces the risk of defects.
Overall, welding automation has numerous applications in various industries. Welding robots are used to weld various components with high precision, ensuring consistent quality. Welding automation also helps to reduce production time and labor costs.
Challenges in Welding Automation
Welding automation can bring numerous benefits to a manufacturing process, such as increased productivity, improved weld quality, and reduced production costs. However, the implementation of welding automation also poses several challenges that must be addressed in order to achieve successful automation. This section will discuss some of the technical, economic, and workforce-related challenges that must be considered when implementing welding automation.
Technical Challenges
One of the main technical challenges in welding automation is the complexity of the welding process. Welding is a highly dynamic process that involves many variables, such as material properties, joint design, and welding parameters. Automating the welding process requires precise control of these variables, which can be difficult to achieve. Additionally, welding automation systems must be able to adapt to changes in the welding environment, such as changes in joint fit-up or material thickness.
Economic Considerations
Another challenge in welding automation is the cost of implementing such systems. Welding automation equipment can be expensive, and the cost of implementing the system may outweigh the benefits if the volume of welding work is low. Additionally, the cost of training personnel to operate and maintain the equipment must be considered.
Skilled Workforce Requirements
Welding automation systems require skilled personnel to operate and maintain them. However, the demand for skilled welders is high, and finding qualified personnel can be a challenge. Additionally, the skills required for welding automation are different from those required for manual welding, and training personnel in welding automation can be time-consuming and expensive.
Integration with Existing Systems
Integrating welding automation systems with existing production systems can also be a challenge. Welding automation systems must be compatible with existing equipment, software, and processes. Additionally, the implementation of welding automation may require changes to existing workflows, which can be disruptive to production.
In summary, while welding automation can bring numerous benefits to a manufacturing process, it also poses several challenges that must be addressed. Technical challenges, economic considerations, workforce-related challenges, and integration with existing systems are all important factors to consider when implementing welding automation.
Future of Welding Automation
Welding automation is expected to play a significant role in the future of manufacturing. As technology continues to advance, it is expected that welding automation will become increasingly prevalent. In this section, we will discuss some of the expected advancements in welding automation.
Technological Advancements
One of the key drivers of welding automation is technological advancements. With the development of new technologies, it is expected that welding automation will become more efficient and effective. For example, advancements in robotics and artificial intelligence are expected to lead to the development of more advanced welding robots that can perform a wider range of welding tasks.
Industry 4.0 and Smart Factories
Another key driver of welding automation is Industry 4.0 and the concept of smart factories. Smart factories are characterized by the integration of advanced technologies such as the Internet of Things (IoT), artificial intelligence, and robotics. In this context, welding automation is expected to play a key role in the development of smart factories. By automating welding tasks, manufacturers can improve efficiency, reduce costs, and increase productivity.
Customization and 3D Printing
Finally, welding automation is expected to play a key role in the development of customization and 3D printing. As manufacturers seek to produce more customized products, welding automation will become increasingly important. In particular, the use of welding robots and automated welding systems is expected to enable manufacturers to produce complex, customized products more efficiently. Additionally, welding automation is expected to play a key role in the development of 3D printing, which is expected to revolutionize the manufacturing industry by enabling the production of complex, customized products on demand.
Overall, the future of welding automation looks bright. As technology continues to advance, it is expected that welding automation will become increasingly prevalent in the manufacturing industry. With the development of new technologies and the integration of advanced technologies such as Industry 4.0 and 3D printing, welding automation is expected to become more efficient, effective, and versatile.
Frequently Asked Questions
How does automation enhance the welding process?
Welding automation enhances the welding process by improving productivity, quality, and safety. Automated welding systems can increase production rates, reduce cycle times, and eliminate human errors. They can also improve weld quality by ensuring consistent weld placement and penetration. Additionally, welding automation can reduce the risk of injury to workers by eliminating the need for manual welding.
What are the different types of welding automation?
There are several types of welding automation, including robotic welding, automated welding machines, and automated welding cells. Robotic welding involves the use of robots to perform welding operations, while automated welding machines use pre-programmed controls to perform welding tasks. Automated welding cells are self-contained units that include all the necessary equipment for welding.
Which industries commonly use welding automation?
Welding automation is commonly used in industries such as automotive, aerospace, construction, and manufacturing. These industries require high volumes of welding with consistent quality, making automation an ideal solution.
What are the benefits of robotic welding over manual welding?
Robotic welding offers several benefits over manual welding, including increased productivity, improved weld quality, and reduced labor costs. Robotic welding systems can work continuously without the need for breaks, and they can perform welding tasks with greater accuracy and consistency than manual welders. Additionally, robotic welding can reduce labor costs by eliminating the need for skilled welders.
How has welding automation evolved in recent years?
Welding automation has evolved significantly in recent years, with advancements in technology and software. Modern welding automation systems are more flexible, easier to program, and offer greater precision than earlier systems. Additionally, welding automation systems are now more affordable and accessible to small and medium-sized businesses.
What considerations are important when implementing an automated welding system?
Several considerations are important when implementing an automated welding system, including the type of welding operation, the size and complexity of the parts being welded, and the required production rates. Other factors to consider include the cost of the system, the availability of skilled labor to operate and maintain the system, and the safety implications of the system. It is important to conduct a thorough analysis before implementing an automated welding system to ensure that it is the right solution for the specific application.